Whether for production, inspections or maintenance, employees performing industrial activities rely on having many different pieces of reference information at their fingertips. Digital assistance systems from Centeract relieve the burden on employees by compiling all available information and displaying it in a user-friendly way – such as through an AR application on their tablet. Thanks to the standardized modules, Centeract applications can be implemented swiftly and tailored to specific use cases.
Centeract platform: Digital assistance systems with augmented and virtual reality
Digital solutions for industrial challenges
In many parts of industry, there is still a long way to go to exploit the full potential of the digital transformation. Companies often deploy software that is not integrated into their existing IT landscape, while some data remains in paper form. As a result, employees and engineers have to trawl through different sources to compile the information they need for their work – which costs valuable time, can lead to errors and has a negative impact on employee satisfaction. What’s more, existing IT systems are not always suitable for visualizing data, which can make it harder for employees to quickly grasp the wider context of their work.
Our Centeract platform has a modular structure and offers numerous applications to relieve the burden on your employees in their day-to-day work – and help them generate more value.
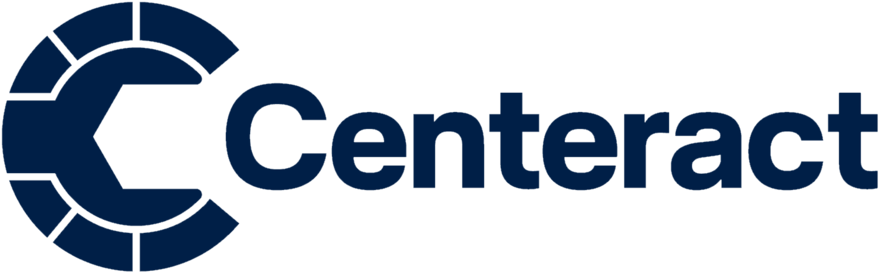
Benefits of digital assistance systems from Centeract
Centeract gives your employees the information they need for their activities – at the right time and in the right place. This saves the effort of searching for information and can make their work considerably more efficient and productive.
Feedback on completed tasks is fully digitalized, meaning that reports can be generated automatically. Individual reports offer transparency, facilitate data-assisted decisions and allow for data-based process analysis. These reports can also help to optimize resource use, ensure compliance with guidelines and promote continuous improvement.
Centeract reduces the human error rate, as its digital assistance systems display current, relevant data at every point.
Centeract takes idle, repetitive tasks – such as searching for information in paper documents and in different systems – off your employees’ hands. This frees them up to concentrate on more demanding activities that generate more value. It can also relieve the burden on individual employees, improve employee satisfaction and reduce workforce turnover.
Digital assistance systems from Centeract can be adapted quickly to changing circumstances or new tasks. In addition to our core modules, we can also develop and integrate additional, fully customized applications to meet your specific needs. This flexibility makes Centeract a cost-effective solution for companies of all sizes.
Thanks to our standardized modules, digital assistance systems can be implemented in next to no time, progressing from proof of concept to the finished product. This means you can soon reap the rewards and increase your value generation.
The digital assistance systems from Centeract can be integrated seamlessly into your system landscape. Interfaces with other systems facilitate smooth data exchange.
Potential use cases for Centeract
Digital assistance systems from Centeract provide support in all sectors with industrial, manual activities. We have developed standardized core modules suitable for the most common use cases, which we can adapt or supplement at any time.
When it comes to manufacturing assemblies, the digital assistance systems from Centeract provide support throughout the product engineering cycle – from design and preparation to production. All information stored in different systems, such as data on individual components in your company’s PLM system, is compiled in a single location. The assistance system can then display data on the designed 3D models along with lists of required components, visualizing them for employees with the help of a 3D viewer.
Centeract digital assistance systems support plant and machinery maintenance by linking all relevant component information with the necessary work steps. The result is digital maintenance instructions that, when combined with AR-capable end devices, can guide employees through the maintenance process, step by step.
Efficient issue management through Centeract applications can support inspections and approvals of products and buildings. Custom templates and checklists can be configured to ensure that defined approval processes are observed. In just a few steps, users can document and define the location of issues in a given environment before exporting the results as a digital report.
In the product engineering phase, designers can amend, supplement and refine products in collaboration with stakeholders by working on virtual reality 3D models. In addition, AR applications allow engineers to check whether the parts they have designed meet requirements and are compatible with other assemblies.
It’s not only your employees who can benefit from visualizing products and assemblies: your customers, apprentices and new recruits can all benefit from the functionalities of Centeract applications.
- When it comes to sales, you can use our virtual reality applications to showcase future products to your customers with the help of virtual reality. This way, you can work with your customers to trial and coordinate on different configurations in a virtual space.
- AR and VR applications can also be used to provide training for employees and apprentices, perhaps to familiarize them with products or the precise steps of a work process.
Do you need a digital assistance system for a specific use case? We would be happy to develop customized modules or configure an application tailored to your requirements.
Our core modules can be tailored to many other use cases.
For example, we developed the PalleTEYZE application for Lufthansa Logistik on the basis of our AR module.
The shipment being prepared for transport is checked against the designated pallets or containers, with any protruding elements highlighted in color. The application also indicates the percentage of the loading volume already taken up.
Centeract: Implementing our digital assistance system
- Numerous successfully implemented digitalization projects involving digital assistance systems
- Extensive process and IT knowledge
- Cross-sectoral experience on in our customers’ industries
- State-of-the-art augmented reality and virtual reality technologies
As a Software-as-a-Service (SaaS) platform, Centeract connects to existing systems and integrates seamlessly into your process landscape.
We’ll accompany you on your journey to a customized assistance system, from the initial idea to proof of concept through to successful, operational use. The journey starts with a detailed analysis of your requirements, processes and IT landscape. Then, we’ll develop user stories, select suitable modules and configure them to your needs before implementing the solution and training your employees to use your new digital assistance system in practice.
Find out more about the Centeract web applications, the native AR and VR applications and the interfaces to the existing IT systems in the company.
Are you interested in digital assistance systems from Centeract?
Get in touch – our expert team would be happy to demonstrate how you could structure your processes more efficiently with Centeract. We look forward to hearing from you!