The “Digital Twin” is one of Industry 4.0’s greatest success stories. For logistics in particular, the real-time, virtual simulation of complex processes can harness huge potential. An interview with Ralf Struckmeier, Vice President of Lufthansa Industry Solutions (LHIND)
Optimize reality with the “Digital Twin”
Mr Struckmeier, what exactly is a “Digital Twin”?
A “Digital Twin”, something we’re familiar with from the engineering industry, among others, is the virtual representation of a real object or process. It is an excellent way of monitoring an object in real time. What’s much more exciting, however, is the fact that various scenarios can be simulated. For example, the “Digital Twin” allows us to exert new parameters on existing processes, let the effects play out virtually, and see what happens.
That sounds perfect for logistics, doesn’t it?
It does, indeed! After all, logistics processes are determined by highly complex interrelationships and dynamics. If even the slightest change to a link in the supply chain is made, the knock-on effects can be substantial. The “Digital Twin” enables companies to map their processes virtually, make changes and, in doing so, tap into real potential for optimization.
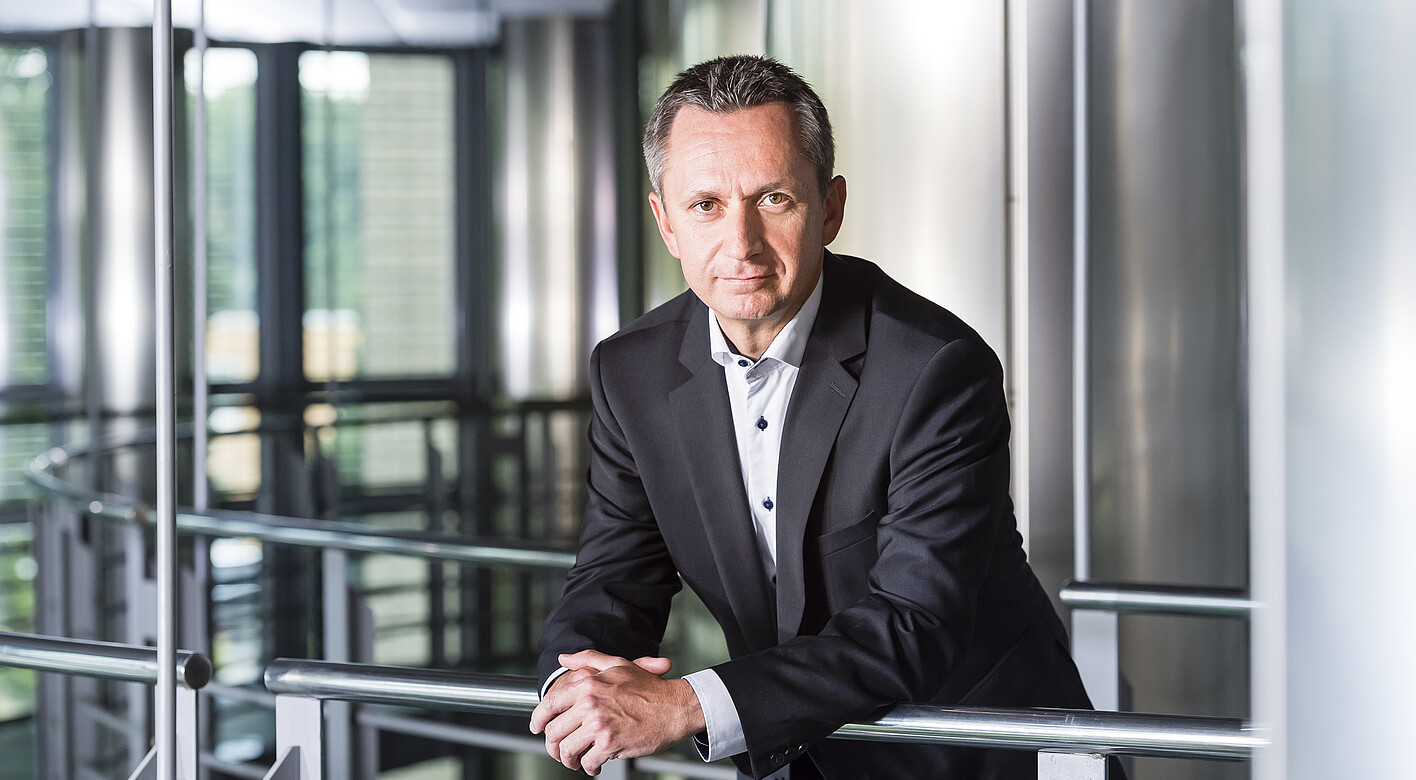
The “Digital Twin” enables companies to map their processes virtually, make changes and, in doing so, tap into real potential for optimization.
Ralf Struckmeier, Vice President Logistics
Theoretically, how can this be implemented?
At the beginning of every supply chain is the distributing company. Let’s assume, then, that a company has to supply several hundred stores worldwide with goods as and when required. This can be complicated. The “Digital Twin” allows the staff responsible to simulate the goods’ individual transit times to each individual store precisely, which, in turn, means that improvements can be made where needed. In international logistics, goods for “long haul” distribution are usually dispatched from the production site via a “hub”, which could be, for example, a port or an airport. Of course, the “Digital Twin” also comes in very handy at these hubs.
How’s that, exactly?
Among other things, the virtual model can be used to calculate the most ideal way to load a container ship. But that’s not all – the way in which the containers are stacked at the port, the “pre-stowage”, can be optimized. The result is that the loading procedure, and the subsequent unloading of the cargo at the destination, can be carried out with maximum efficiency.
What about for “short haul” consignments or the last mile?
The “Digital Twin” comes into its own here, too, for example in real-time route optimization – depending on the situation, time pressure and traffic situation, dispatchers can prioritize individual vehicles. Those that transport perishable goods, for example, are fast-tracked, whereas other vehicles can wait a little longer. This completely new level of information and transparency also leads to a reduction in CO2 emissions. This is because, if we can estimate with accuracy which trucks, ships, planes, etc. will and won’t make their arrival slots at the world’s major goods hubs on time, we can slow down many transport routes greatly – indeed, as the “race” to make the arrival slots on time decreases, so will fuel consumption. This reduction in consumption is where the great sustainability potential of logistics digitalization lies.
How does Lufthansa Industry Solutions implement the “Digital Twin” for its customers?
This differs on a case-by-case basis. Large enterprise companies usually have the necessary resources in place already, which is why we regularly take on an advisory role with them. Medium-sized companies, on the other hand, often require us to accompany them throughout the entire process, ranging from problem definition to proof of concept and, ultimately, to implementing the “Digital Twin” solution. The fact that we at LHIND are able to offer everything from a single source is always a tremendous advantage.